کوره های عملیات حرارتی چیست؟
کوره عملیات حرارتی انواع مختلفی دارند که می توان آن ها را به روش های مختلفی مثل نوع گاز (الکتریکی و شعله ای)، اتمسفر کوره (گاز خنثی، خلاء، بدون گاز محافظ، گازهای ایندوترمیک)، دمای کاربری و نوع عملیات حرارتی دسته بندی کرد.
انواع کوره های عملیات حرارتی
1- کوره حمام نمک
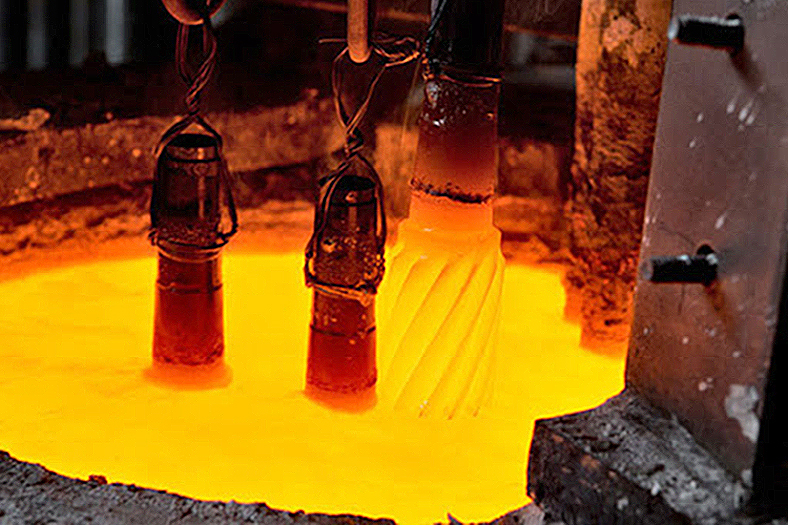
کوره های حمام نمک کوره های هستند که برای عملیات حرارتی مختلف از قبیل سختکاری ، کربن دهی ، نیتروژن دهی مورد استفاده قرار می گیرند. مکانیزم کلی این کوره ها بدین شکل است که در یک محفظه استیل، نمک ذوب شده و به دمای مطلوب عملیات حرارتی می رسد و قطعات درون آن قرار گرفته و در زمان مناسب در محلولی مانند روغن کوئنچ می شوند.
قدمت این کوره ها زیاد بوده ولی همچنان در صنایع مختلف از آنها استفاده می شوند علت استفاده از این کوره ها به علت یکنواختی سختی ، یکنواختی دما ، عدم اکسید شدن ، عدم ایجاد اعوجاج می باشد .
از مشکلات استفاده از این این نوع کوره ها نیاز به حمام نمک متفاوت برای هر نوع فرایند، دشوار و هزینه بر بودن تمیز کردن نمک از روی قطعات پیچیده و استفاده از حمام نمک سیانوری در برخی از فرایندها (مانند کربوراسیون) است که میتواند برای اپراتورها و محیط زیست زیانآور باشد.
2- کوره های شعله ای (سوخت مایع یا گاز)
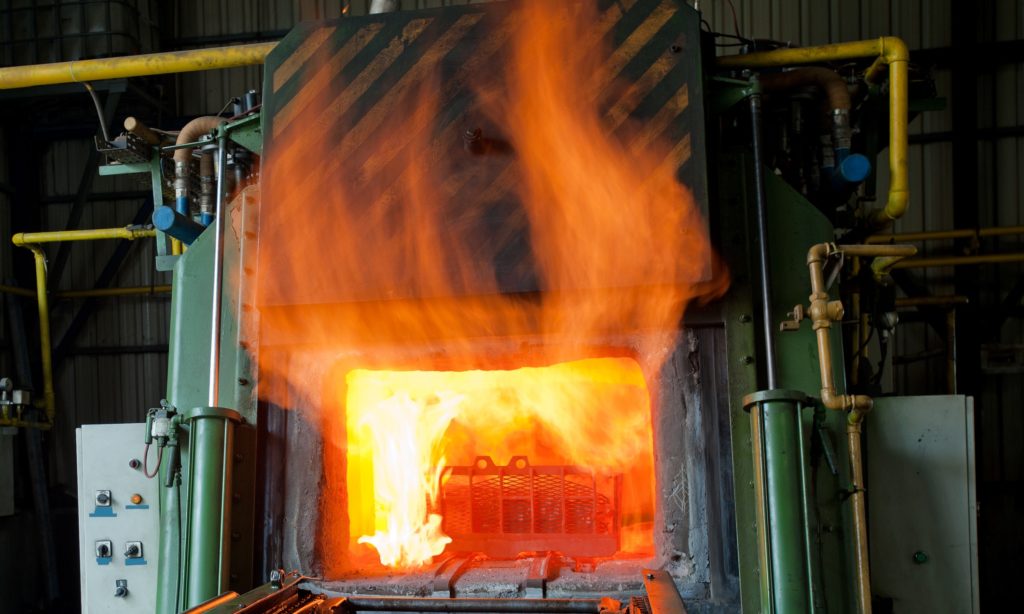
در این نوع کوره ها محفظه گرمایش و بنابراین، قطعه هایی که باید عملیات حرارتی شوند، توسط شعله گرم می شوند. سوخت مورد استفاده می تواند یک گاز قابل احتراق (مانند گاز طبیعی) و یا یک سوخت مایع (مانند گازوییل) باشد. از بین کوره های سوخت، کوره های گازسوز بهترین و مقرون به صرفه ترین هستند. کوره های گازسوز از نظر طراحی ساده هستند و کنترل بهتری بر دما دارند و تا دمای 1500 درجه سانتیگراد قابل استفاده هستند. کوره های گازسوز را می توان از کوچکترین تا بزرگ ترین اندازه طراحی کرد.
3- کوره های برقی
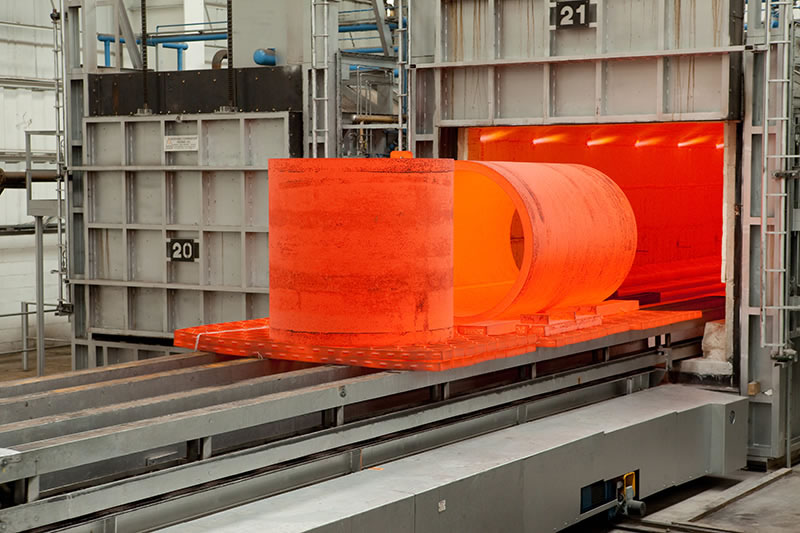
کوره های الکتریکی امروزه بیشتر مورد استفاده قرار می گیرند و جایگزین کوره های گازسوز می شوند. کوره های الکتریکی مزایای بسیاری دارند. طراحی بسیار ساده، عدم نیاز به استفاده از محفظه احتراق، مجرای گاز، و دودکش های پشته ای، یکنواختی دما در کوره ها و کنترل دقیق دما را می توان به راحتی با استفاده از اتوماسیون انجام داد. کوره های الکتریکی شامل کوره های مقاومت الکتریکی، کوره های القایی و گرمایش لیزر و پلاسما است.
4- کوره های مقاومت الکتریکی
از میان روش های گرمایش الکتریکی، کوره های مقاومت الکتریکی رایج ترین کوره های مورد استفاده برای عملیات حرارتی فلزات و آلیاژها هستند. همچنین در کوره های گرمایش مقاومتی می توان دما را به راحتی و با دقت بالایی کنترل کرد. توضیحات مربوط به این کوره ها در بخش کوره های ذوب آورده شده است.
5- کوره گرمایش القایی
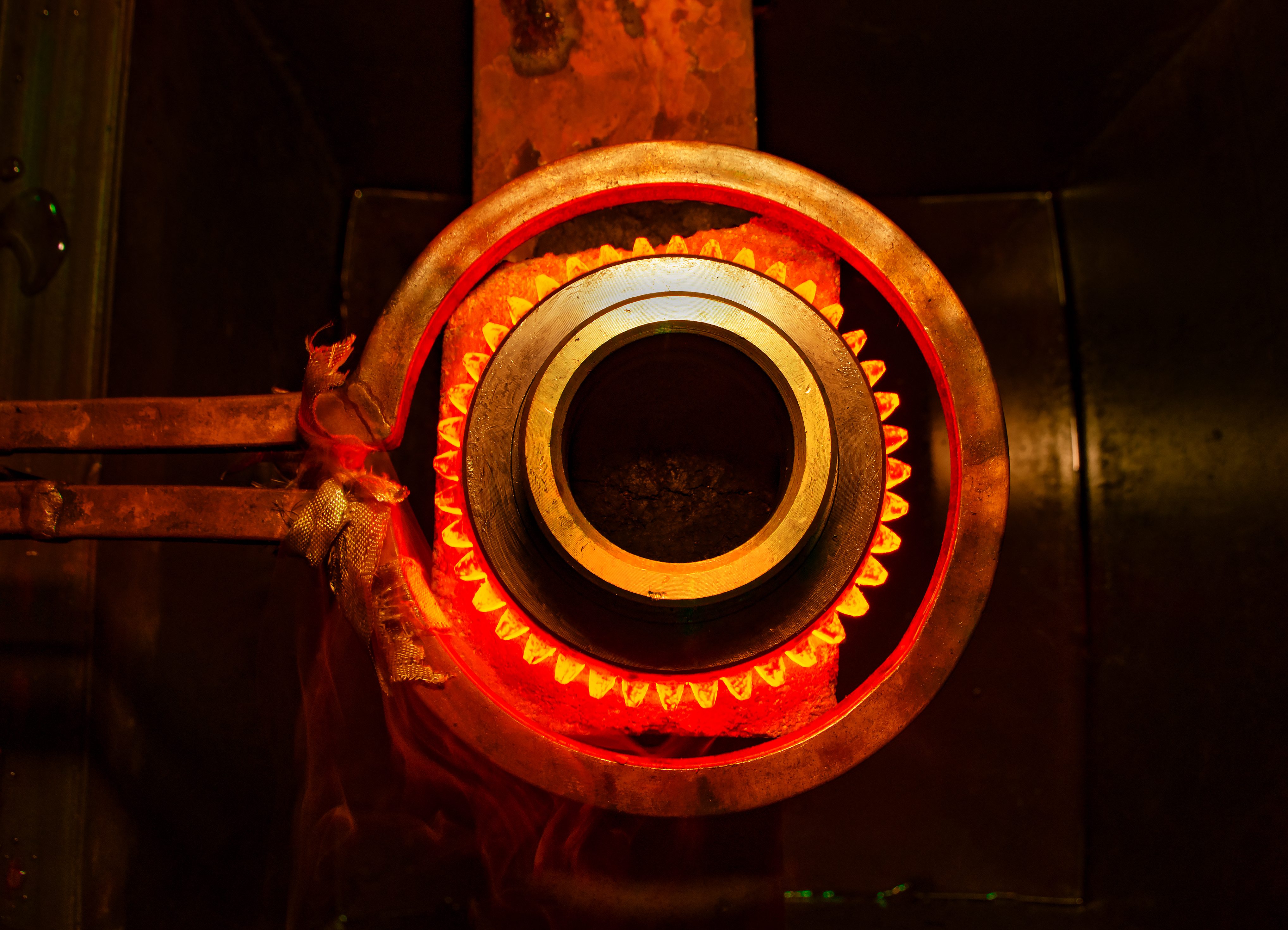
کوره گرمایش القایی که زیرمجموعه کوره های برقی است، رایج ترین، کامل ترین و حتی ارزان ترین روش سخت کاری سطحی (در تولید انبوه قطعات مشابه) است. در این روش حرارت دادن سطح به کمک یک سیم پیچ هادی که از آن جریان متناوب با فرکانس زیاد (در محدوده 50-2 کیلوهرتز) عبور می کند، انجام می شود. سختی و ضخامت پوسته آستنیته شده بستگی به فرکانس جریان داد.
هرچه فرکانس جریان بیشتر باشد عمق نفوذ جریان و بنابراین، ضخامت پوسته سخت شده کمتر خواهد شد.
6- کوره های اتمسفر کنترل شده
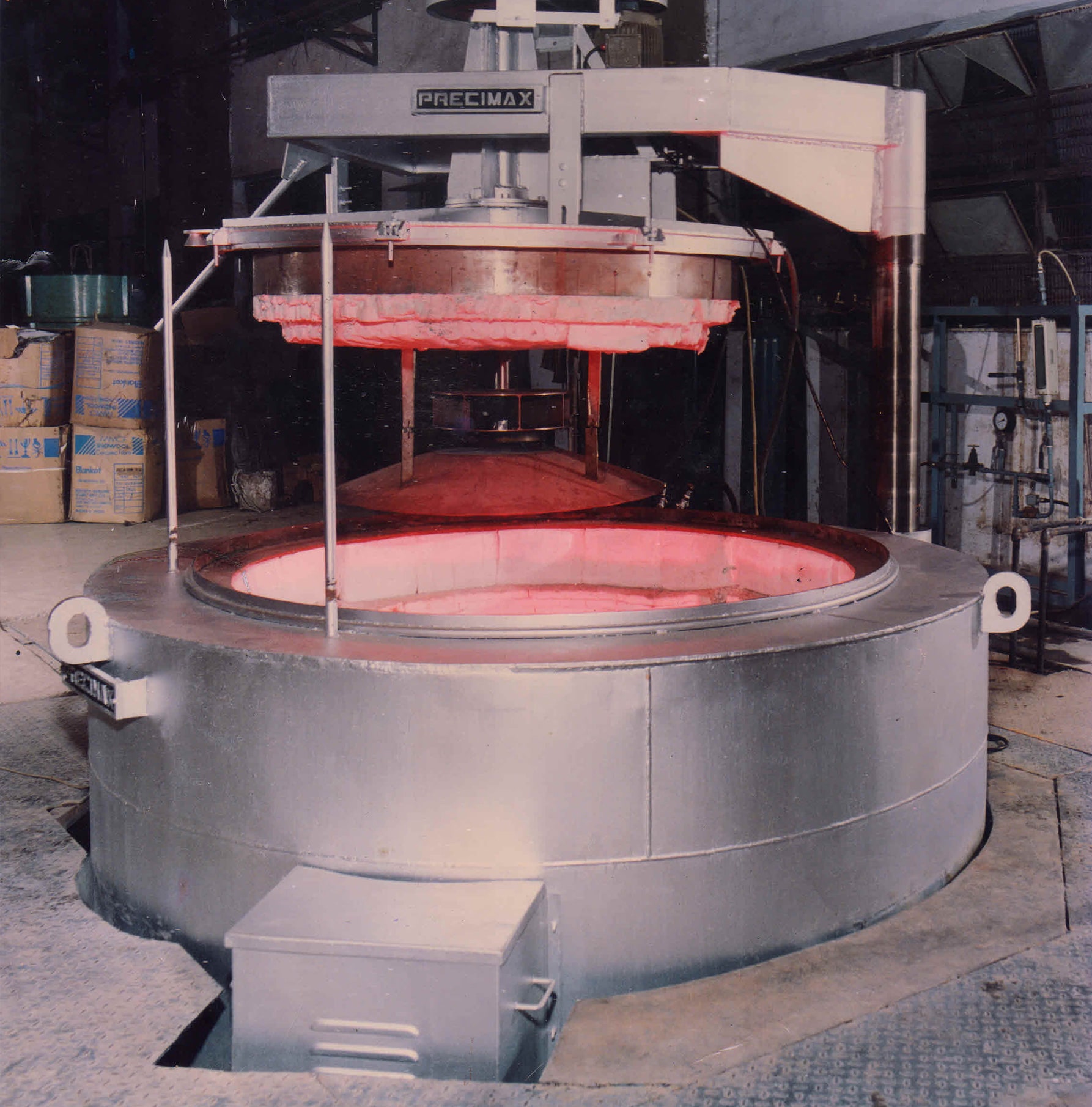
در این نوع کوره ها از گاز های محافظ استفاده می شود. عملیات حرارتی ابزارها و قطعه های گران قیمت در این نوع کوره ها، هم از نظر اقتصادی و هم از جنبه های کاربردی یکی از بهترین و مناسب ترین روش ها است. برای رسیدن به بهترین خواص و حداقل آسیب به سطح قطعات، نیاز به استفاده از اتمسفر محافظ در محیط کوره میباشد.
با توجه به اینکه فولادها دردمای بالا آمادگی لازم جهت اکسیداسیون را دارد در صورتی که کوره دارای اتمسفر محافظ نباشد در حین عملیات حرارتی سطح قطعه پوسته کرده و سیاه میشود.
برای جلوگیری از این مشکل از اتمسفر محافظ استفاده میشود. کورههای با اتمسفر کنترل شده از پرکاربردترین کوره های عملیات حرارتی هستند و قابلیت انجام تمامی فرآیندهای عملیات حرارتی را دارا میباشند.
5- کوره های خلا
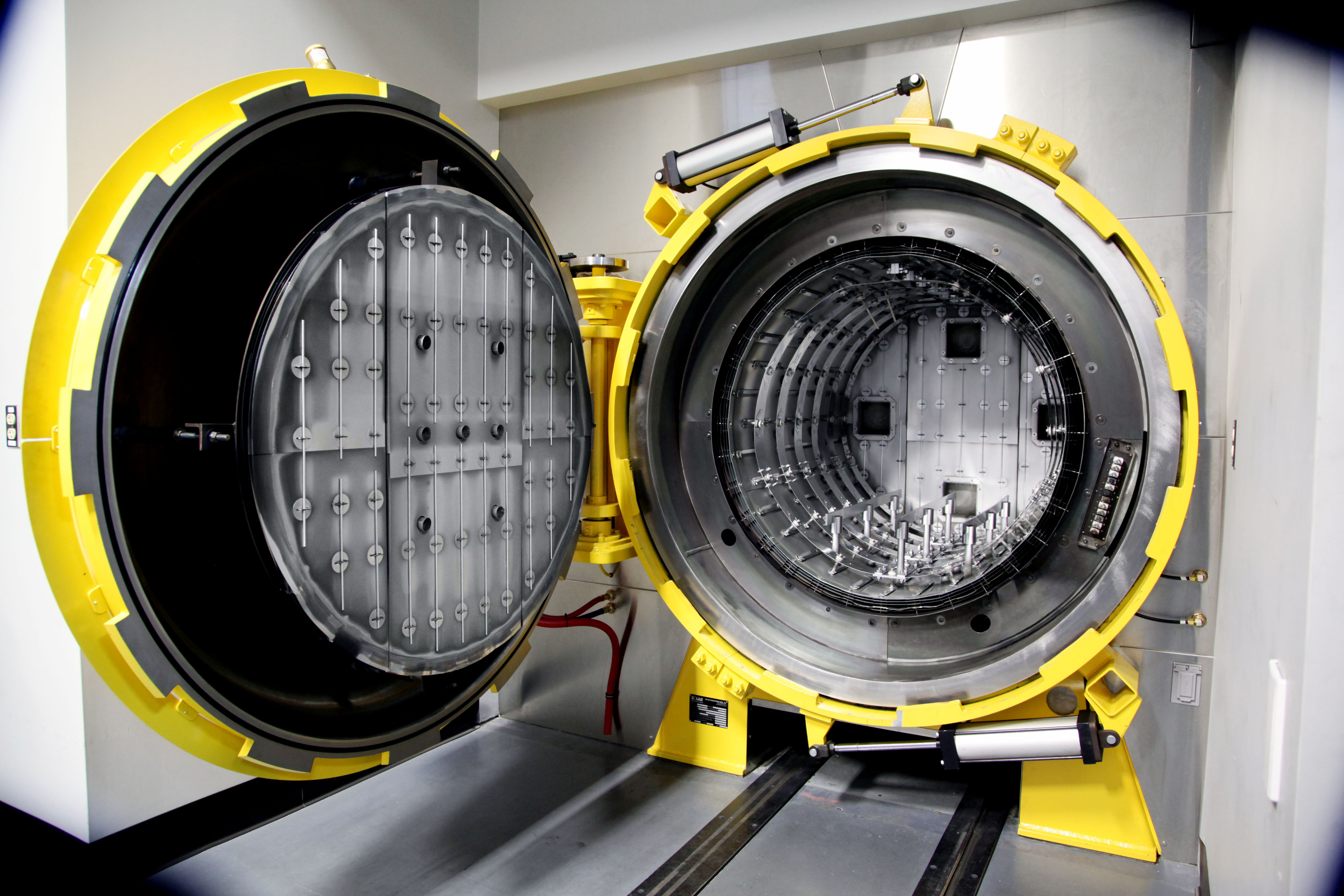
خلا محیط مناسبی برای عملیات حرارتی فولادهای مقاوم به حرارت و پرآلیاژ است. در این روش فشار هوا در حدود 2- 10 تور (میلیمتر جیوه) قابل قبول است. از جمله مزیت های خلا، آلودگی کمتر آن نسبت به محیط های دیگر عملیات حرارتی است.
از این رو، هیچ نوع تغییر ترکیب شیمیایی سطح در این روش رخ نخواهد داد. به عبارت دیگر افزایش و یا کاهش کربن سطح قطعه ها و یا اکسایش آن ها را نخواهیم داشت و پس از عملیات حرارتی سطوح قطعه به طور کامل تمیز و براق اند.
برخلاف محیط های محافظ دیگر که اغلب قابل انفجارند، خلا هیچ نوع خطر انفجاری ندارد. همچنین برخلاف حمام های نمک که بیشترشان سمی هستند، خلا هیچ نوع مسمومیتی ایجاد نمی کند.
مهم ترین اثر جانبی نامناسب خلا، احتمال تبخیر برخی از عناصر الیاژی است که در خلا های بسیار زیاد فرارند. افزون براین، در عملیات حرارتی خلا، انتقال حرارت محیط انجام نمی گیرد، بلکه فقط توسط تشعشع انجام می شود. این امر ممکن است به گرم و سرد شدن غیریکنواخت قطعه به ویژه در دماهای پایین منجر شود.
6- کوره های پیوسته (Continuous)
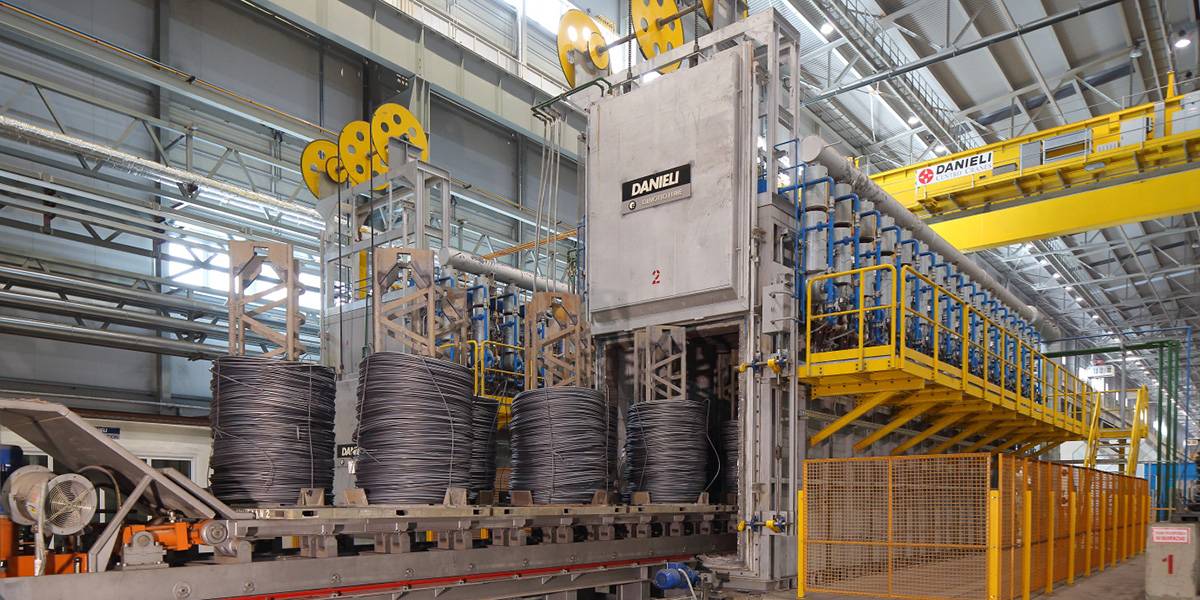
در بسیاری از کارخانجات و صنایع، کوره های عملیات حرارتی به دو نوع مداوم (continuous) و غیر مداوم تقسیم بندی می شوند. کورههای غیر مداوم یا تک شارژ به کوره هایی اطلاق میشود که بعد از شارژ مواد و بسته شدن درب کوره، سیکل از پیش تعیین شده عملیات اجرا میگردد و کورههای مداوم اساساً کورههایی هستند که در آنها مواد از یک طرف شارژ و عملیات حرارتی صورت می گیرد.
از طرف دیگر تخلیه می شوند و اکثراً برای عملیات حرارتی قطعات ریز مانند پیچ و مهره استفاده میگردد. به همین دلیل این کورهها برای عملیات انبوهی از قطعات مشابه مناسب است.
.
- ۰ ۰
- ۰ نظر